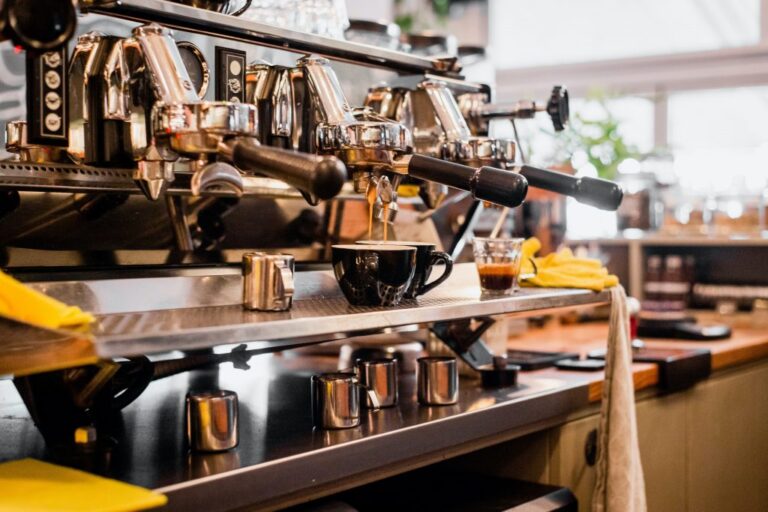
Сколько еще кофе может приготовить наша машина, прежде чем потребуется техническое обслуживание? Что ж, это фундаментальный вопрос для большинства членов ЭЛЕДИА. Очевидным ответом на это может быть «мы узнаем, когда он сломается». Но если оборудование имеет фундаментальное значение в производственной линии, допустимы ли неожиданные простои для технического обслуживания?
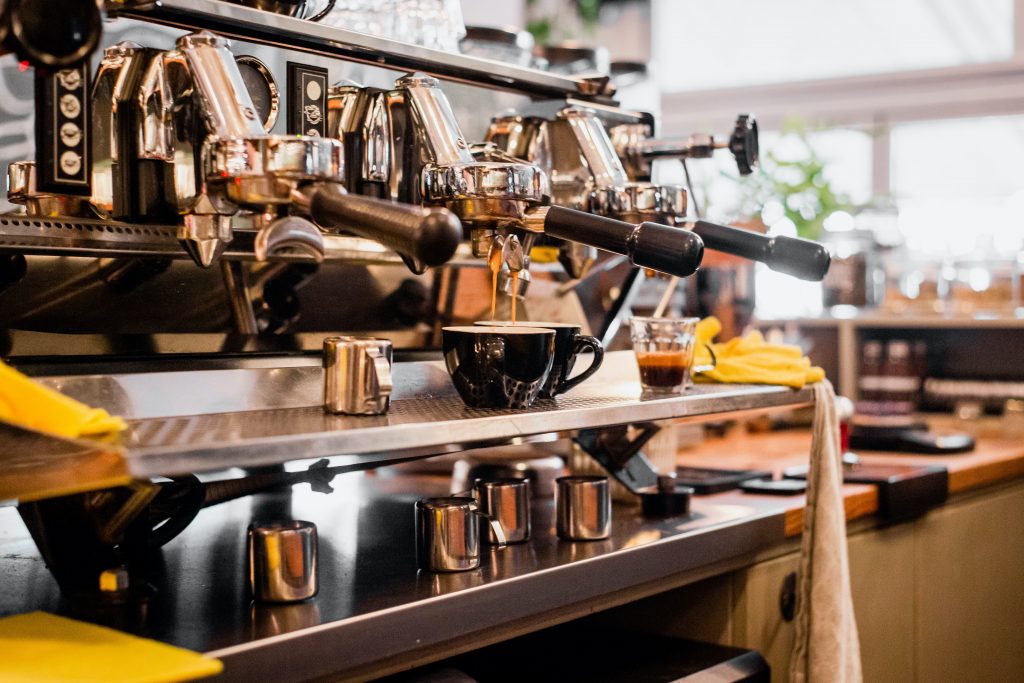
В рамках терминологии технического обслуживания, ремонта и капитального ремонта (ТОиР) описанный ранее подход (замена/техническое обслуживание оборудования после отказа) будет называться корректирующее обслуживание, и известно, что это приемлемая стратегия только в том случае, если производственный процесс можно прервать в любой момент с минимальными последствиями (кстати, это НЕ относится к кофемашине ELEDIA). Совершенно противоположная стратегия заключается в том, чтобы запланировать техническое обслуживание после того, как было выполнено заранее определенное количество циклов / часов работы, следуя концепции профилактическое или плановое обслуживание. Поскольку проверки проводятся на периодической основе, эта стратегия имеет очевидное преимущество, заключающееся в гарантировании фиксированных затрат. Но минимальны ли такие затраты? В эпоху умных заводов и Индустрия 4.0ответ на такой вопрос может быть менее очевиден.
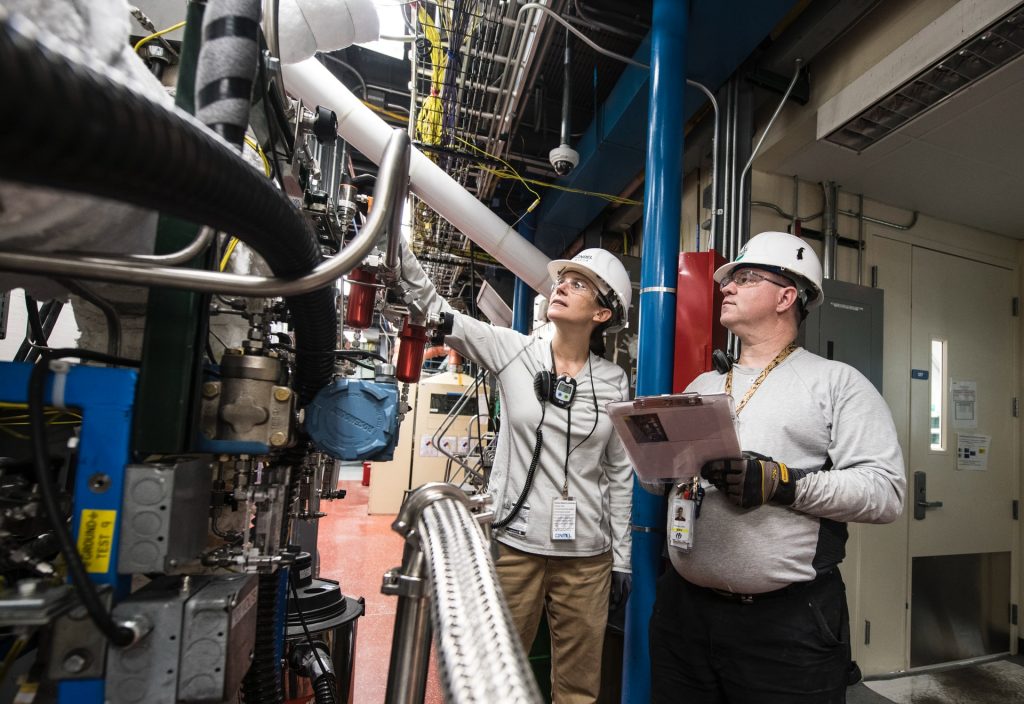
Свести к минимуму затраты на техническое обслуживание, заранее зная, когда именно произойдет отказ оборудования или процесса, всегда было мечтой руководителей промышленных процессов. Профилактическое обслуживание на самом деле стало одним из наиболее конкретных применений Индустрии 4.0 для осуществления этой мечты. Основная цель профилактического обслуживания — определить состояние оборудования/процесса, чтобы определить, когда техническое обслуживание действительно необходимо. В этом смысле оно отличается от профилактического или корректирующего обслуживания, поскольку оно основано на фактическом прогнозировании состояния оборудования (прогнозирование на основе данных), а не на ожидаемом среднем сроке службы (прогнозирование на основе статистики) или на обнаружении уже произошедших аварий. Проблема (диагностика). Единственным недостатком является то, что предсказание будущего обычно не выглядит простой задачей.
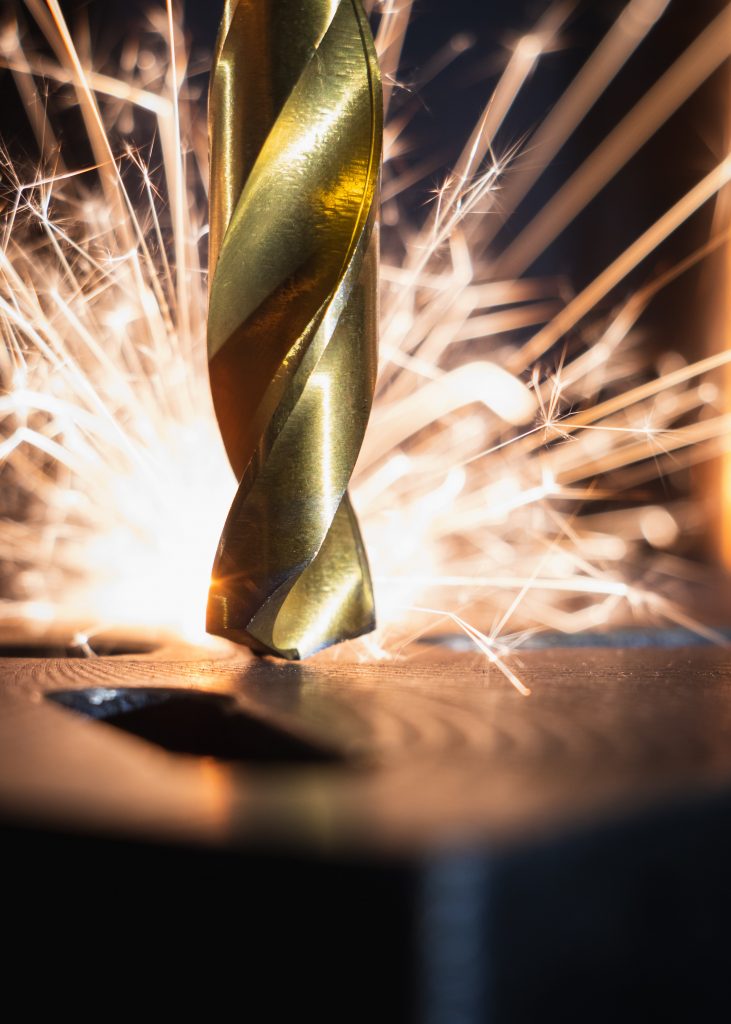
Современные системы автоматизации оснащены множеством датчиков, позволяющих наблюдать за состоянием машин и процессов. Более того, доступность недорогих развертываемых беспроводных датчиков и парадигма IoT еще больше расширяют возможности получения подробных данных из сложных систем, даже работающих на крупных заводах, а также сбора таких данных для дальнейшей удаленной обработки. Тем не менее, возникает простой вопрос: могу ли я понять, сколько циклов точно выполнит станок для резки по звуку его вращающихся лезвий? Вот где в игру вступает ИИ.
В последние годы члены ELEDIA разработали, применили и внедрили широкий набор Методологии ИИ для Индустрии 4.0 сценариев как в малых, так и в больших масштабах, разрабатывая инструменты прогнозирования и профилактического обслуживания, которые применялись как к отдельным машинам или производственным процессам, так и к крупным заводам, размещенным в отдельных помещениях. Фундаментальный подход, которого придерживается ELEDIA для достижения высокоточных и эффективных прогнозирующих возможностей, представляет собой сочетание как физического понимания фактического процесса/машины, находящегося под наблюдением, так и расширенных возможностей анализа и обучения, обеспечиваемых искусственным интеллектом. Интегрируя знания об ожидаемых физических характеристиках исследуемого процесса (например, взаимосвязь между частотой основного тона/спектром звука, издаваемого вращающимся лезвием, и режимом вращения, разрезаемым материалом и скоростью резки) и настраивая искусственный E-AIR интеллектуальных методологий была продемонстрирована возможность раннего обнаружения аномалий в производственных процессах и надежных заблаговременных предупреждений о техническом обслуживании. С этой целью было проведено «объединение» данных ключевых показателей эффективности (KPI) и информации, собранной с помощью нескольких различных технологий неразрушающей оценки и неразрушающего контроля (таких как измерения уровня звука, акустический анализ, анализ давления и вибрации, измерения температуры/влажности). фундаментальная задача, которую необходимо решить.

В этом сценарии недавнее применение пакета E-AIR Industry 4.0 было связано как с автоматическим анализом состояния состояния оборудования, так и с контролем производственного процесса в промышленном сотрудничестве с Группа ИМАмировой лидер в разработке и производстве автоматических машин для обработки и упаковки фармацевтических препаратов, косметики, продуктов питания, чая и кофе.
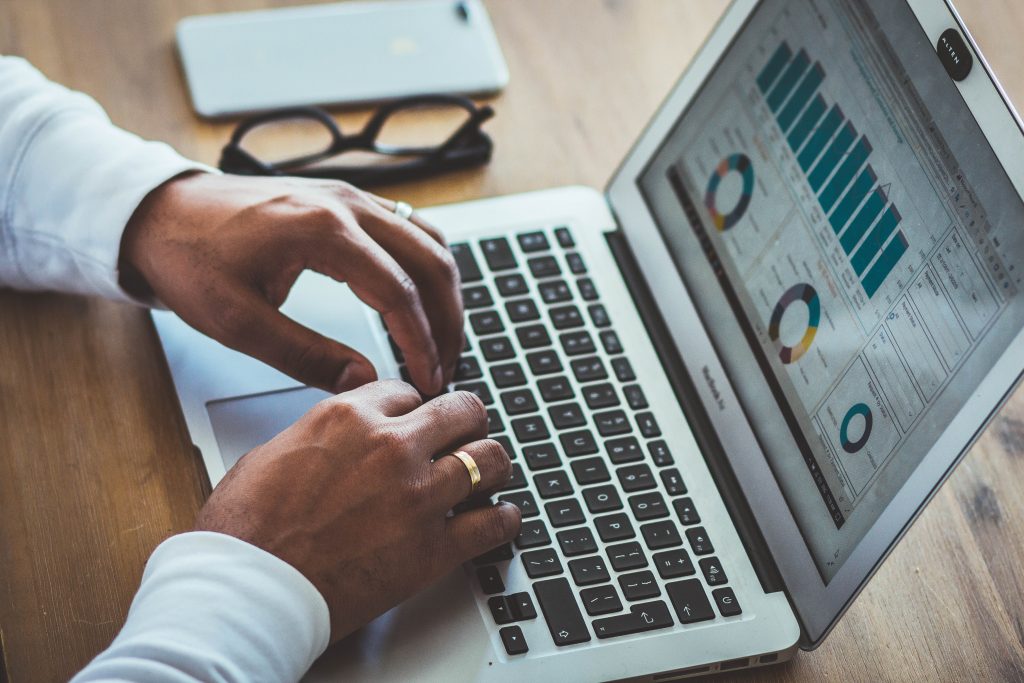
Текущие исследовательские усилия в ELEDIA направлены на дальнейшую настройку методологий E-AIR Industry 4.0 Suite для объединения данных, анализа данных и машинного обучения для более сложных сценариев профилактического обслуживания на основе моделей. В этой связи возможность самообучения Цифровой двойник аналог реальной системы/процесса машинного оборудования уже был продемонстрирован членами ELEDIA в практических промышленных сценариях, и его обобщение для решения крупномасштабных задач на нескольких предприятиях в настоящее время находится в стадии разработки.
Так что в следующий раз, когда кто-то спросит: «Сколько еще кофе может приготовить наша машина, прежде чем потребуется техническое обслуживание», E-AIR придет на помощь.
Больше информации
Для получения дополнительной информации о наших демонстрациях и программных пакетах ИИ для Индустрии 4.0, пожалуйста, свяжитесь с нами по адресу contact@eledia.org.
связанные проекты